
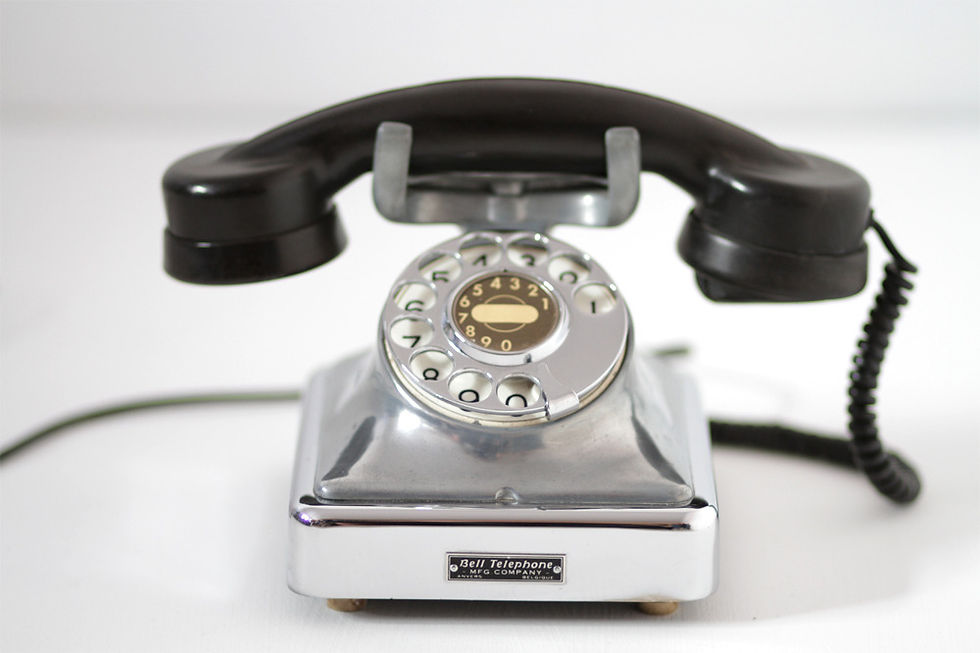



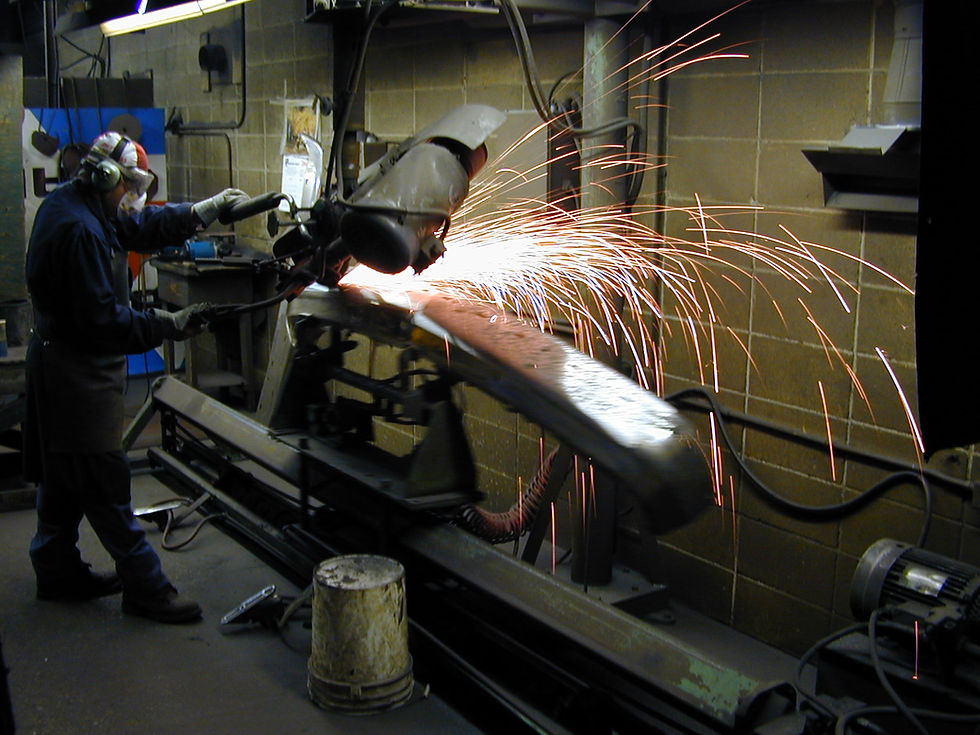


PLATING PROCESS
Surface engineering is a hot topic these days, with applications throughout a wide range of industrial sectors. Engineering surface treatments and coatings can bring specialist properties of corrosion and wear resistance, without compromising the characteristics of the substrate or base metal. Many new processes are emerging, their innovations and developments sometimes outpacing any proven industrial demand or performance demonstration. There is vapor deposition, implantation, an expansive array of thermal spray coatings, and many others, all attempting to attain the ultimate hard, tough, wear resistant, low friction and anti-corrosion surface.
01
STRIPPING
Stripping. Parts are stripped to bare metal; all paint, dirt, oil and grease, rust, old plating and any other foreign material must be removed. Items brought to us stripped clean will cost less to plate then if we perform the stripping step (sand blasting is a typical method for stripping parts).
02
POLISHING
Polishing. Polishing is the removal of surface metal using a series of abrasive wheels and sanding belts (at any plating shop, the words "sand," "grind" and "polish" basically mean the same thing). We start by using coarse-cutting grinders, working down to soft cloth buffs. The end result is a high-gloss polished metal part with all pitting, scratches and impurities removed.
03
WIRING & RACKING
Wiring and Racking. We use hooks, racks, copper wire and other methods to hold parts in the plating tanks; this also provide electrical contact to the part.
5. Cleaning. Parts must be surgically clean before plating -- the slightest spec of dirt, grease, oil, buffing compound, rust, or other foreign matter will cause a reject. In our shop we use an elaborate series of soap, acid and water solutions to guarantee a clean, spotless surface.
04
CLEANING
Cleaning. Parts must be surgically clean before plating -- the slightest spec of dirt, grease, oil, buffing compound, rust, or other foreign matter will cause a reject. In our shop we use an elaborate series of soap, acid and water solutions to guarantee a clean, spotless surface.
05
COPPER PLATING & BUFFING
Copper Plating and Buffing. Parts are copper plated and then buffed to a brilliant shine. This is an important step in the process, as copper offers an added layer of corrosion protection and helps to fill-in polishing lines and pits. (While copper is very thin, many layers of coppering and sanding can slowly build-up surfaces. In fact, copper can be used to level and fill much like a painter uses primer and block sanding.)
06
WIRING, RACKING & RE CLEANING
Wiring, Racking and Re-cleaning. The processes of steps 4 and 5 are repeated before nickel plating.
07
NICKEL PLATING
Nickel Plating. It is the nickel which provides the deep luster of a chromed part, in addition to providing another layer of protection for long-lasting chrome. Parts remain in our nickel plating tank for about an hour.
08
COPPER PLATING & BUFFING
Chrome Plating. Chrome, the final plating step, is actually a protective coating over the shiny nickel which prevents the nickel from tarnishing.
10. Final Inspection. Parts are cleaned and inspected; some parts may require minor buffing.
09
FINAL INSPECTION
Final Inspection. Parts are cleaned and inspected; some parts may require minor buffing.